Prototype Making
- Anna
- Apr 6, 2019
- 3 min read
As mentioned in my previous blog post, we had to hand in our project information for the DJCAD catalogue and website. This included an image of our work. I thought that that was the perfect opportunity to do a trial shoot for my one great image and test out different ideas. I started off by taking photos of the knife being used in action. I got Arooj to cut up a clementine and attempted to test out the best angles for such a picture.
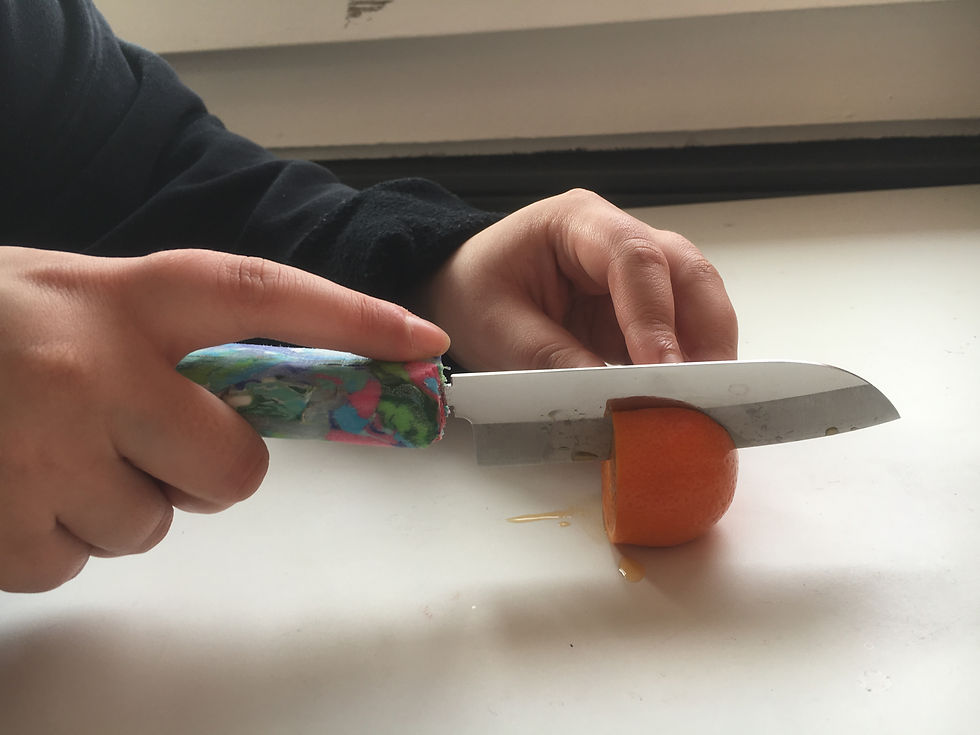
At first, I thought it was important to show how the knife was used because these one great images are so powerful when you see the product “in action”. However, I realised that this type of shot is not very successful for my product. I want my focus to lie on the knife handles, but these are exactly what people cover while holding a knife.
Therefore, after some research of knife product shots, I decided to show my knife within the kitchen environment, but without the human interaction in it.
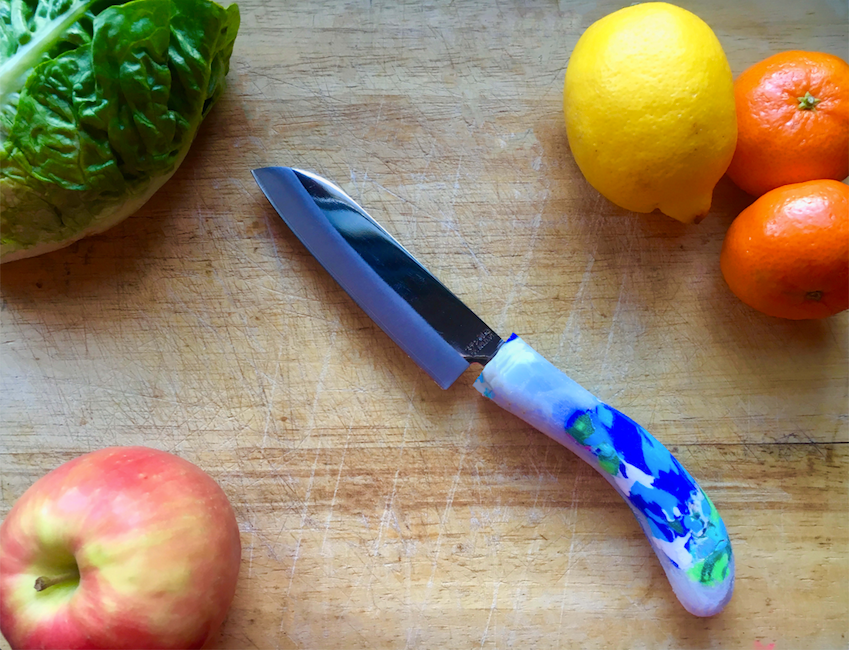
Personally, I really like these shots. The focus lies on the handle, while still providing information about the environment and the use of the knife. I think for my final one great image, I will recreate a version of this shot.
At the beginning of the week, I also had to remake one of the moulds, since one side broke in half again. Once that was dry, I used the moulds to make colourful prototypes. I had previously decided on colour combinations for each individual knife blade. Since I have three different knives in one set, I want every knife to have a different colour combination. However, I did not want to just assume that these combinations would look good in a handle shape, which is why I made prototypes.

This was great because I realised that the colour combination “dark blue – light blue – white” and “dark green – light green – white” work well together, but the combination of all green and blue tones does not fit in with the other two ones. Therefore, I decided to add white into the last combination, hoping that another colour present in all three would visually connect them better.
With this colour knowledge, I then went on to make further prototypes, but this time I inserted the knife blades as well.

Throughout this week, I also continued working on my brand. While I had decided on a name, I had not yet designed a logo. I decided on a simple, bold font. I wanted a minimalistic visual that not only expressed professionalism, but also made it easy to read the name. Along with the font, I added a circle in the background, connecting the letters “Z” and “A”. This is supposed represent how Ozean takes old products and makes a totally new product out of that waste. It emphasises the cycle of repurposing and recycling.

At the end of the week I also had my last tutorial with Polly. This was very helpful for me since I was able to sort out final questions I had for my project and the hand-in. Particularly when it came to the booklet, I was not sure whether I should mention how my product idea changed from a table to knife handles, or whether I should solely talk about the knife handles. Additionally, our products are supposed to incorporate elements of design, technology and people, each having a different weighting. I was a bit worried, since my product does not showcase any digital technology elements. However, Polly reassured me that my manufacturing method is a form of technology.
Polly also gave me useful advice for my branding. She stated that the plastic that I somehow want to incorporate into the packaging should not only link to the colour combinations of the knives, but I should also make sure they fit well with the bamboo aesthetic of the box. As well as that, she said that my brand colours for the logo should also be directly linked the colours present in the knife handles.
For the viva, Polly advised me to use all my photographic evidence in a slideshow. I have made a lot of prototypes, so Polly recommended to take a small selection of them while beaming up a picture of all prototype. Additionally, she encouraged me to start thinking about possible manufacturing processes for batch productions, since that could be a possible question asked during the presentation. All of these tips were very useful for me to prepare for the hand-in and the presentation and eased my stress a little.
Comments